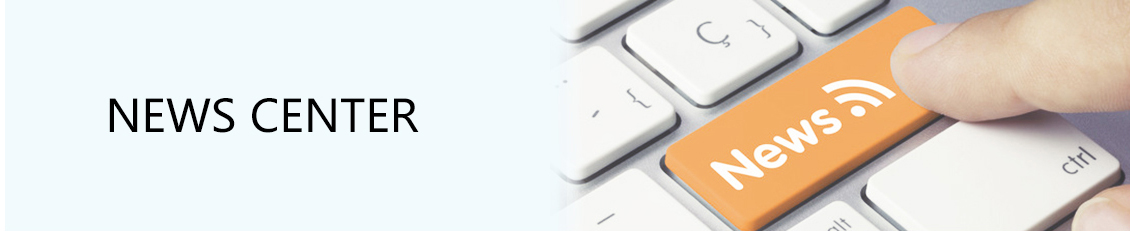
研究背景:
目前,液态食品热加工过程中主要使用高温蒸汽或高温热水作为热源,通过热传导的方式将热量自外至内传递给物料,这一过程不仅热效率低,还会使管壁附近物料被过度加热,在影响物料品质的同时,导致管壁出现结焦、结垢现象,这不仅增加了设备就地清洗难度及强酸、强碱的消耗量,也为实现能源节约、环境友好型食品加工过程带来了重重阻碍。
微波加热作为新型物理场热加工方式之一,是解决上述问题的有效方法。微波的体积加热特性在避免产生高温热表面的同时,也能够使能量靶向作用于目标液体,极大地提升能量利用效率。然而,在现有改善措施中,使用微波加热替代这一过程的研究却鲜有报道,其主要原因是在微波系统中,包括谐振腔尺寸、食品几何形状及放置方式、辅助零配件的使用在内的多个因素都对电磁场分布产生显著影响,不仅会直接影响物料的加热效果,还会导致磁控管击穿等问题。此外,通过常规试验手段很难监测微波场分布与液态食品介电特性之间的关系,从而无法准确预估不同液态食品的微波加热效果,加之微波设备制造成本较高,众多不确定因素极大地限制了微波技术在液态食品加工领域的应用与推广。
研究目的与方法:
计算机仿真模拟技术的进步,为微波设备的发展提供了新的动力。在目前已报道的众多新型微波加工设备中,计算机仿真模拟技术已成为其开发过程中的重要辅助工具。现有研究充分证实计算机仿真模拟技术能够更加全面且真实地揭示电磁场与介电材料之间的复杂耦合关系,在推进微波技术与食品工业的交融发展过程中具有重要意义。本研究使用仿真模拟的方法,对新型连续化液态食品微波加热系统的加热效果进行模拟分析,比较体积流量、微波输入功率、微波频率等因素对液体热响应的影响,并通过试验方法进行模型准确性验证,旨在建立液态食品微波热响应预测模型,推动液态食品热加工过程的微波绿色化替代。
研究结果:
流体热量吸收过程与谐振腔内电场分布紧密相关,电场分布模式决定液态食品加热过程中的温度分布模式,并且高场强区域有利于提高该区域附近的流体升温速率。此外,快速升温区域能够通过流体传热的方式来提升管路内部其它区域的加热效果,体积流量与输入功率的改变间接影响介电加热与流体传热对热响应过程的贡献,微波频率变化直接影响加热效果。通过仿真模拟能够综合考虑上述多种因素,对连续化微波加热过程进行合理预测。
本研究建立的适用于连续化微波加热过程的多物理场耦合模型,能够准确预测这一过程中液态食品热响应效果,在深入理解流体微波加热过程电磁-热耦合过程的同时,也有助于推进微波加热技术在液态食品加工领域的应用,对实现绿色、清洁、可持续的液态食品热加工具有重要意义。